Bus product renders
I produced 3D renders of Nexport’s product portfolio to support the nascent sales and marketing team. These renders were used in a range of communications, including LinkedIn, brochures, investor presentations, and on exhibition collateral. Internally, I used these renders to illustrate new design directions.
Process
I modelled most critical parts from scratch, using technical drawings and actual buses in our workshop for reference. Where possible, I imported 3D CAD models but these proved often both too detailed and yet of poor visual quality. For the first bus I covered, I spent approximately three weeks to complete the renders. Of that time, two weeks were spent modelling with the first week dedicated to obtaining measurements, references, etc.
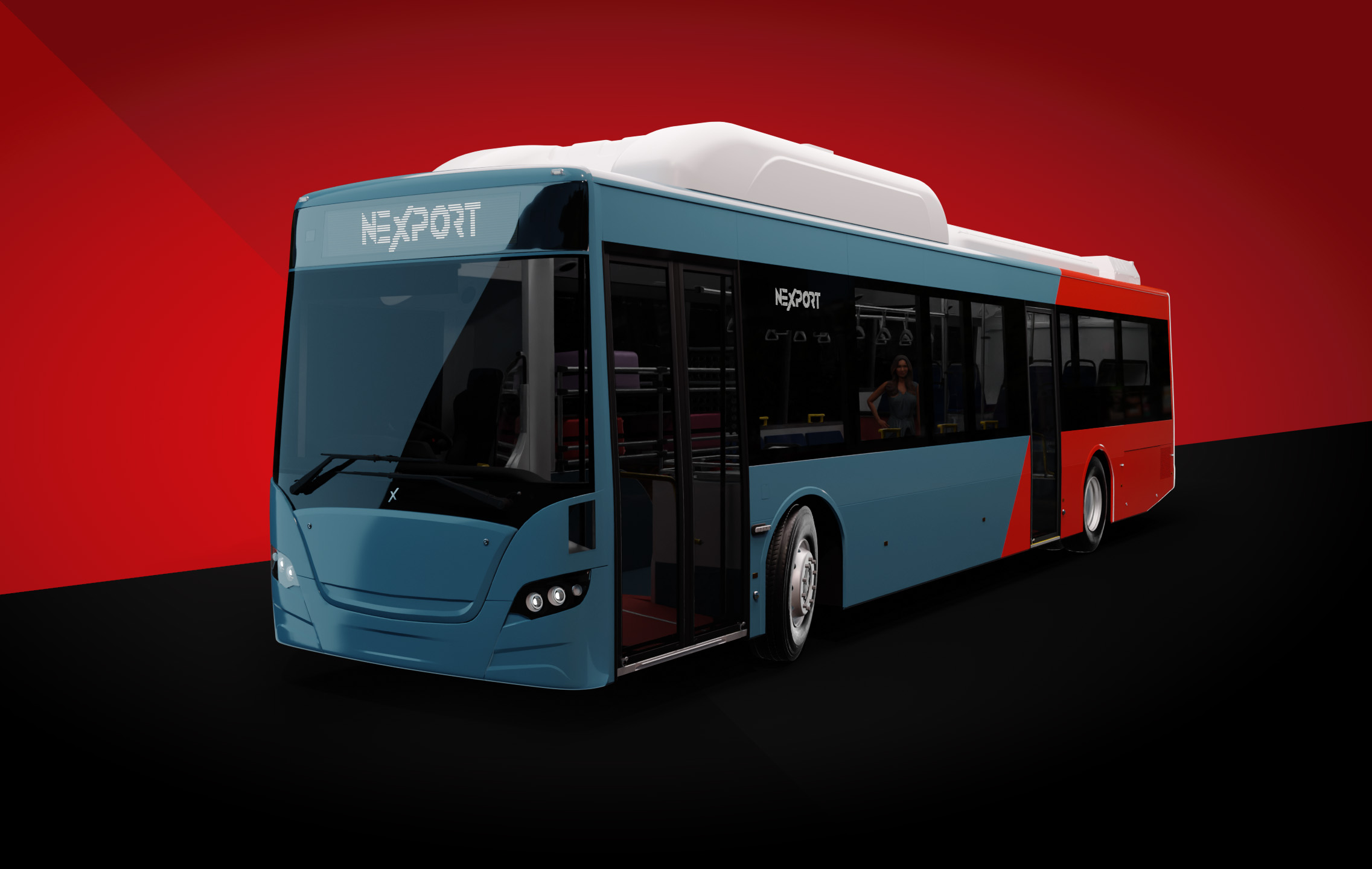
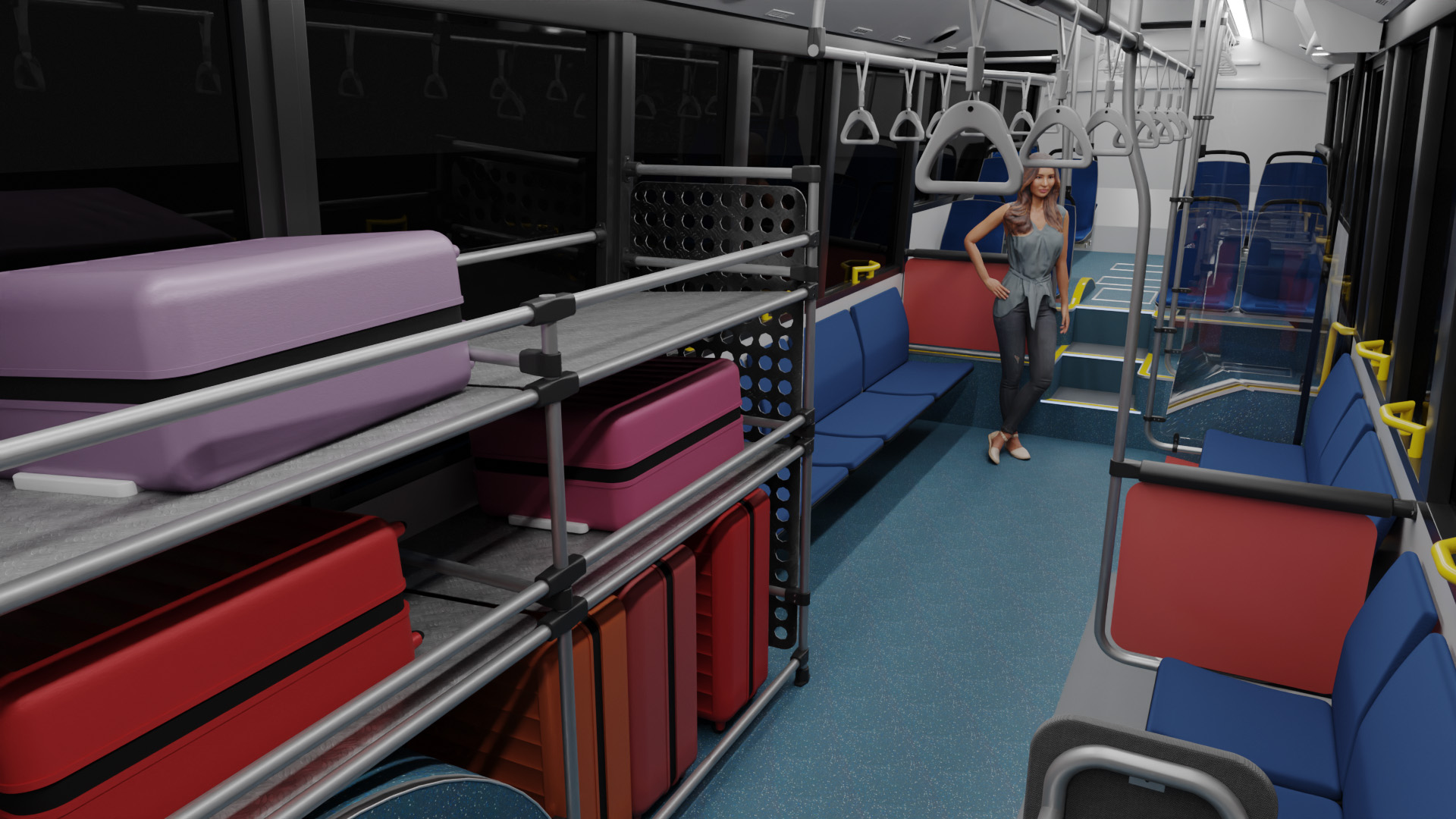
Asset library
All modelling was done in Blender, while making extensive use of an ever-growing library of 3D models and materials. For example, wheels and tires are reused between vehicles. Using a parts system like this made it easy to build new variations or even draft vehicles from scratch. Reusing models also helps to reduce complexity and pressure on computer hardware.
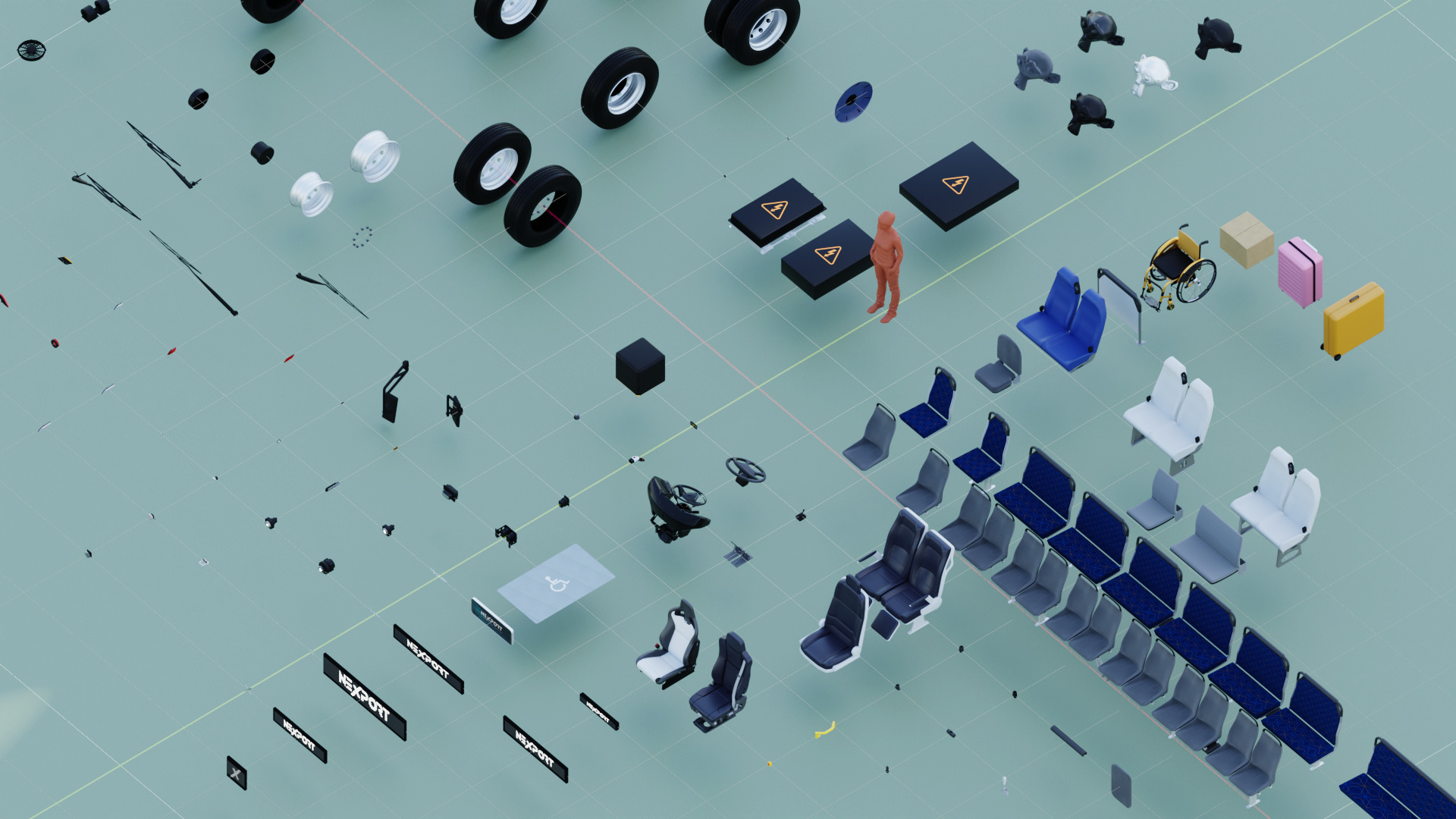
Managing others
Occassionally, I managed contracted 3D modellers to deliver assets to enable faster or concurrent deliveries. One example involved a technical study for an electric concrete mixer truck. Challenging due to high expectations on practical loads, Nexport sought further investment to develop this vehicle for the Australian market. Using technical info provided to me, including a rough layout of major components, I made some quick sketches to get the major shape down. There was no time for detailed design, so while a contractor began his work on a model, I made a very simple 3D model to communicate the key dimensions and shapes. Combined with geometric data from the OEM cab and chassis supplier, this allowed the contractor to progress. Every few days, I received visual updates which I annotated to guide the contractor towards the final result. My responsibility was to ensure both visual quality and timely delivery to allow the CTO and commercial team to continue their negotiations.
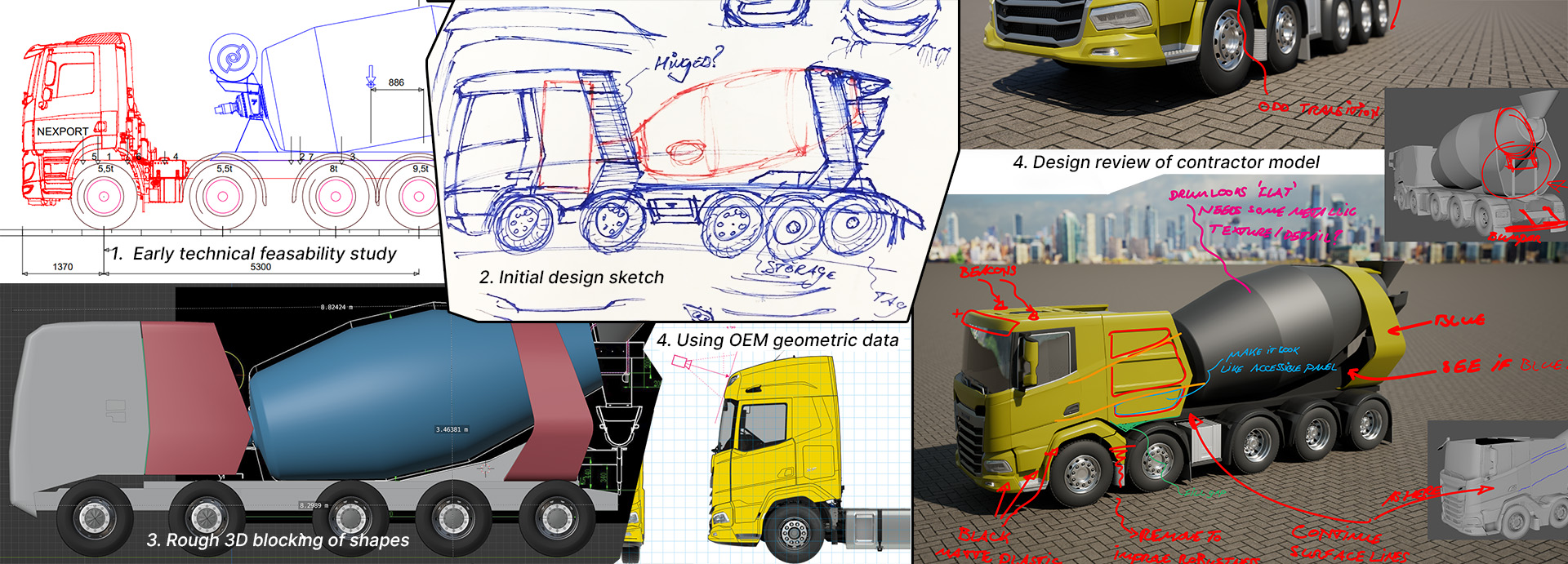
Long after the contractor completed his work, I used the provided models to generate variations as the technical discussions progressed. Axle layouts, battery size and their locations would vary, necessitating model changes. I used Blender as a fast concepting tool, allowing me to iterate quickly (compared to more rigid tools like SolidWorks). Given the primary use of these renders as discussion tools, we did not devote time to staging models in typical use environments, so the render below is an exception to the norm.
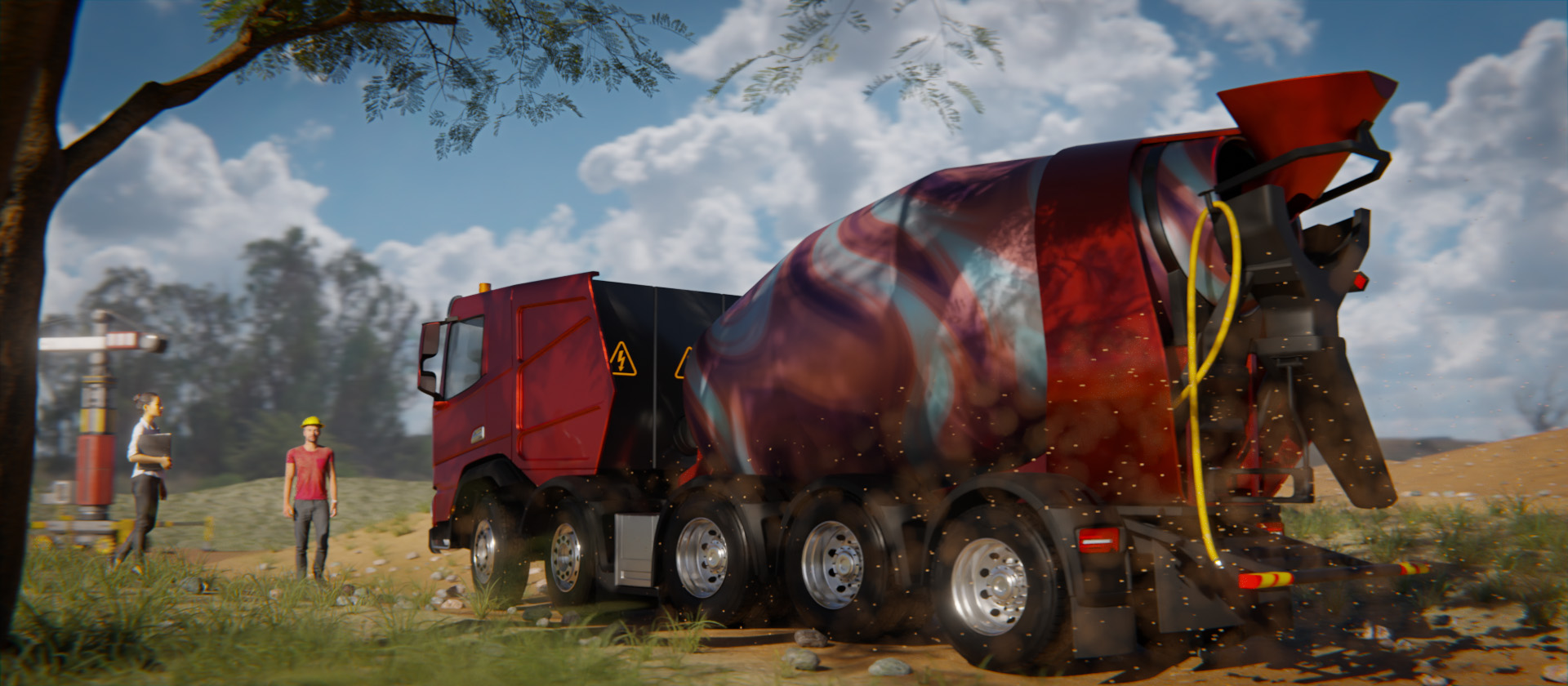
More examples

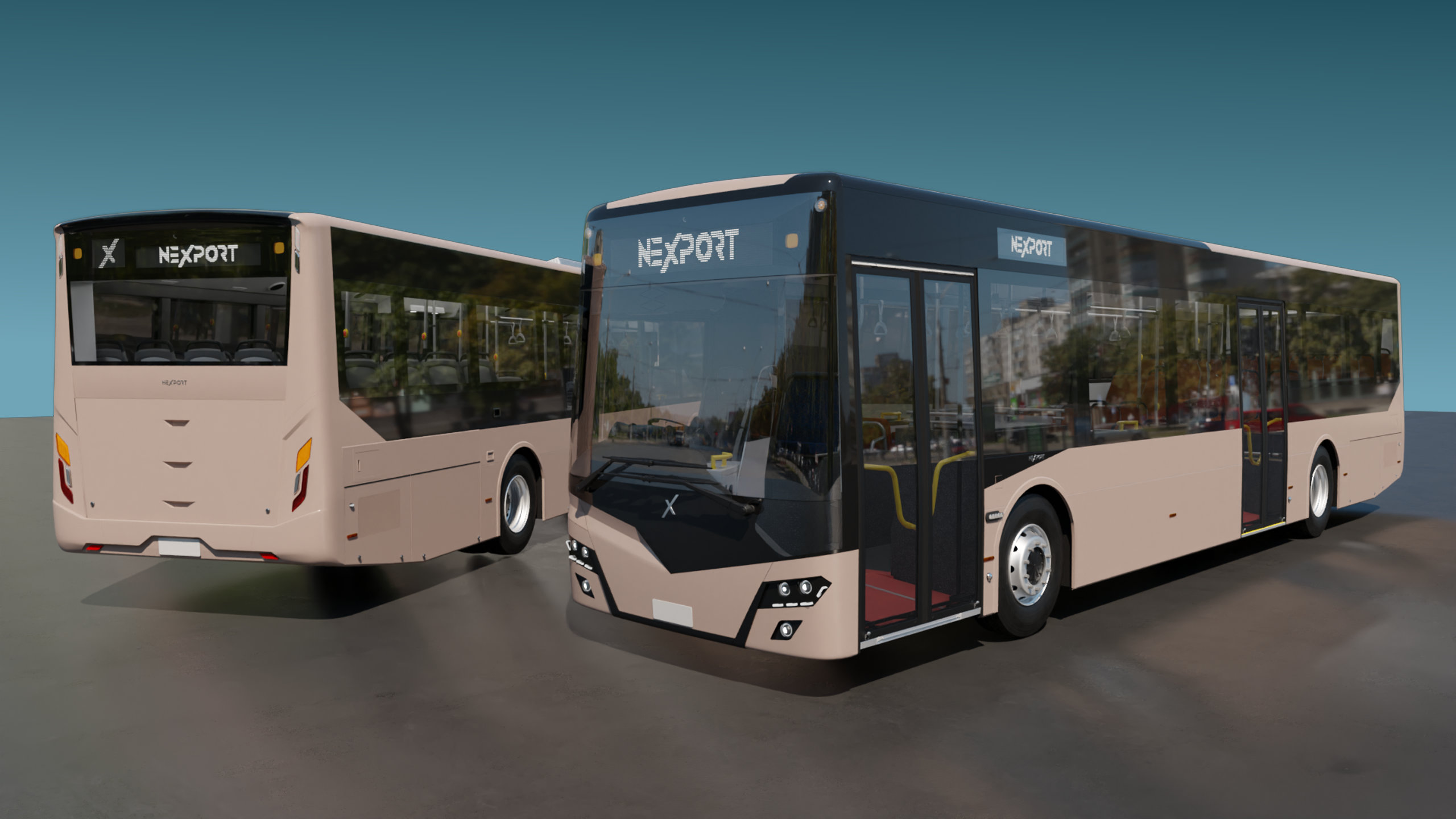
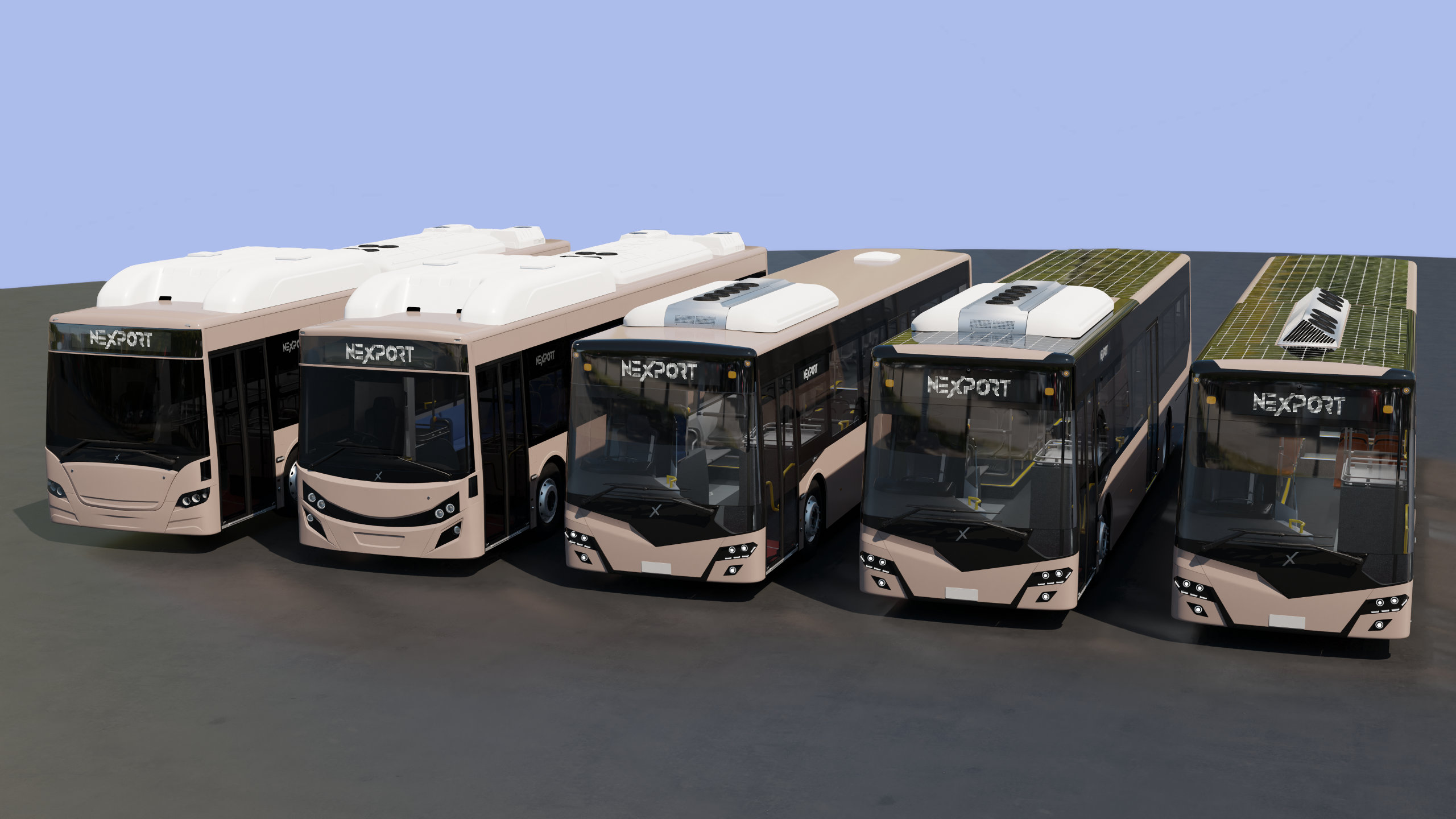
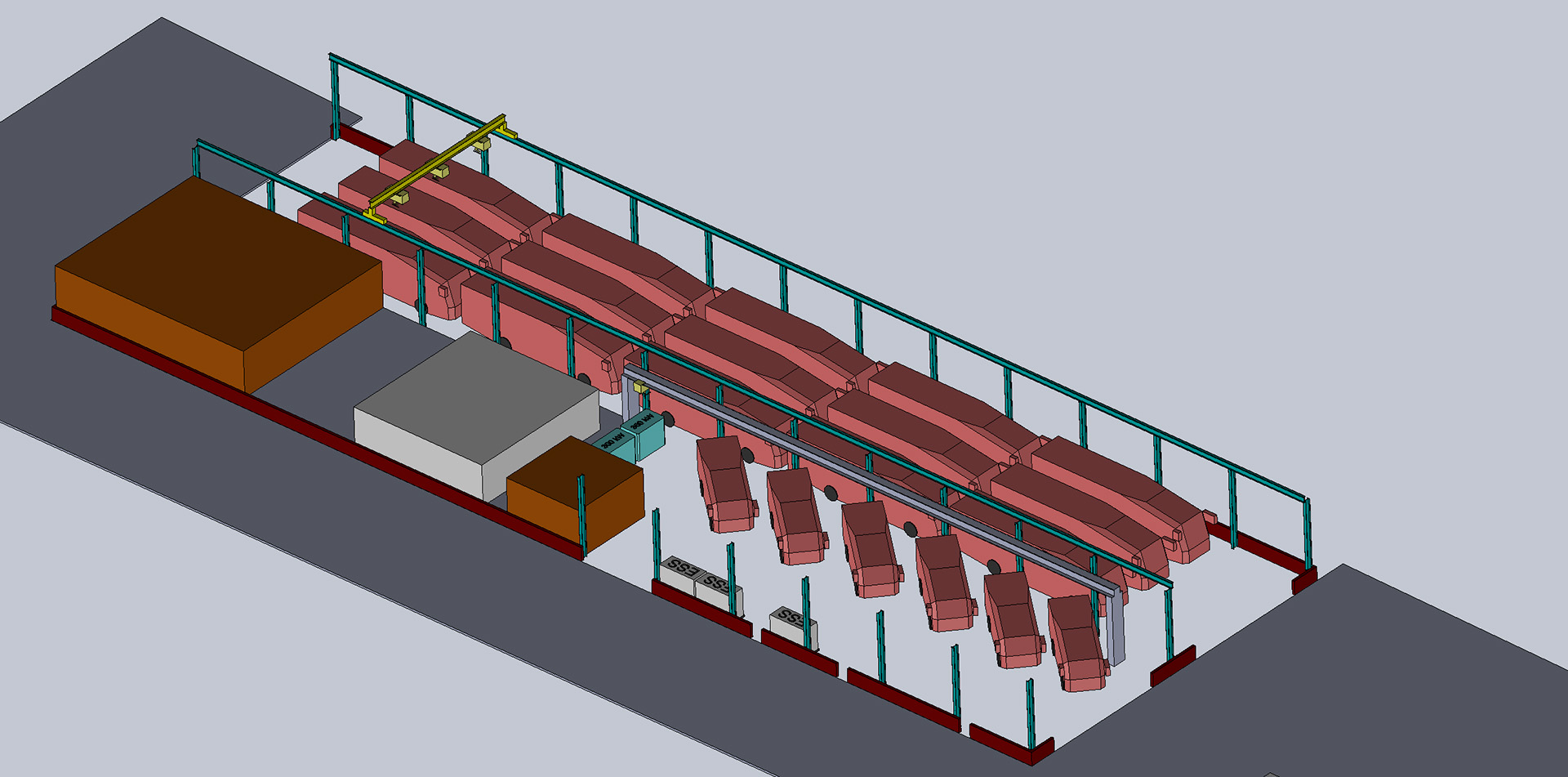